Sponsored article
How do I maintain my sealer machine?
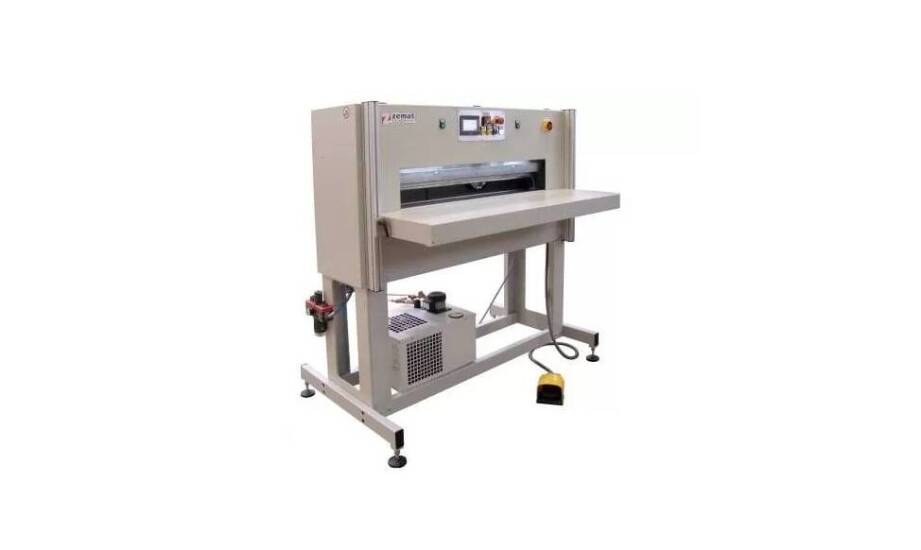
Regular technical inspections are required to keep the equipment running smoothly and trouble-free. Verification of key components allows early detection of possible faults before they lead to more serious problems. Checking of the components responsible for heating, pressure and the control system makes it possible to maintain high seal quality.
Cleaning and decontamination
During operation, the machine comes into contact with various plastics, which leads to the deposition of contaminants on its surface and working parts. Regular cleaning of the heating plates, electrodes prevents the accumulation of residual materials that can affect the process quality. For the removal of deposits, agents adapted to the specific nature of the equipment are used, avoiding substances that could damage delicate parts. Cleaning after each production run makes it possible to maintain full efficiency and eliminates the risk of failure due to the accumulation of residual plastic. The sealer machines are included in the offer of the Zemat Technology Group.
Cooling system check
Efficient operation of the cooling system affects the performance and durability of the machine. Insufficient heat dissipation can lead to overheating of components, which reduces the quality of the joints made and can lead to damage. Check the condition of the cooling hoses regularly. Moving parts, such as guides, hinges or pressure mechanisms, require periodic lubrication to minimise friction and avoid accelerated wear.
Replacement of worn components
During prolonged use, some parts of the machine can wear out, affecting its efficiency. Electrodes, dies should be inspected regularly and replaced when signs of excessive wear are noticed. It is advisable to use original spare parts, as their proper fit affects the quality and safety of the work. Postponing the replacement of worn components can lead to failures that result in longer downtime and higher repair costs. Zemat Technology Group offers sealer machines.
Appropriate parameter settings
Each type of plastic requires precisely chosen sealing parameters, such as operating current, cycle time, pressure force and electrode temperature. For high-frequency sealing, the stability of the RF frequency (e.g. 27.12 MHz) and the even distribution of the electromagnetic field are also crucial. Incorrect settings can accelerate wear of key components and lead to a reduction in the quality of finished seals. It is a good idea to calibrate the device regularly to ensure that the parameters comply with the requirements of the production process. Optimising the settings affects the stability of the machine and minimises the risk of malfunctions.